When it comes to maintaining bearings, one of the most important factors to consider is the amount of grease needed. Proper lubrication is crucial for ensuring that bearings perform optimally and have a long lifespan. But how much grease is actually needed? Unfortunately, there is no one-size-fits-all answer to this question, as the amount of grease required will vary depending on factors such as the type and size of the bearing, as well as the operating conditions it experiences.
In this blog post, we’ll explore the different factors that affect how much grease is needed in a bearing to help you find the right amount for your specific application.
Understanding Grease Lubrication
When it comes to understanding grease lubrication, one key element to consider is how much grease should be used in a bearing. The amount of grease needed will depend on various factors such as the size of the bearing, the operating temperature, and the speed at which it rotates. A common mistake is to over-grease bearings, which can lead to issues such as overheating and premature failure.
On the other hand, insufficient lubrication can cause the bearing to wear out and result in costly repairs. It’s important to follow the manufacturer’s recommendations for the amount of grease to use and to apply it evenly across all surfaces. Regular maintenance and monitoring can ensure that the correct amount of grease is being used and that the bearing is functioning optimally.
By paying attention to this critical factor, you can extend the lifespan of your bearings and improve the overall performance of your equipment.
Types of Grease and Their Properties
Grease lubrication is a popular method of reducing friction and wear in machinery, but not all greases are created equal. There are various types of grease on the market, each with different properties and characteristics suitable for different applications. Lithium-based grease is one of the most commonly used types, known for its high melting point and water resistance.
On the other hand, synthetic grease is ideal for extreme temperatures and high-speed applications, while silicone grease is popular for its compatibility with plastics and rubber. Other types of grease include calcium-based, aluminum complex, and polyurea, each with their unique set of properties that make them suitable for various applications. When choosing a grease, it’s essential to consider factors such as the application, load, speed, temperature, and desired service life.
Understanding the properties of different types of grease can help you select the best option for your equipment, ensuring optimal performance and extended lifespan.
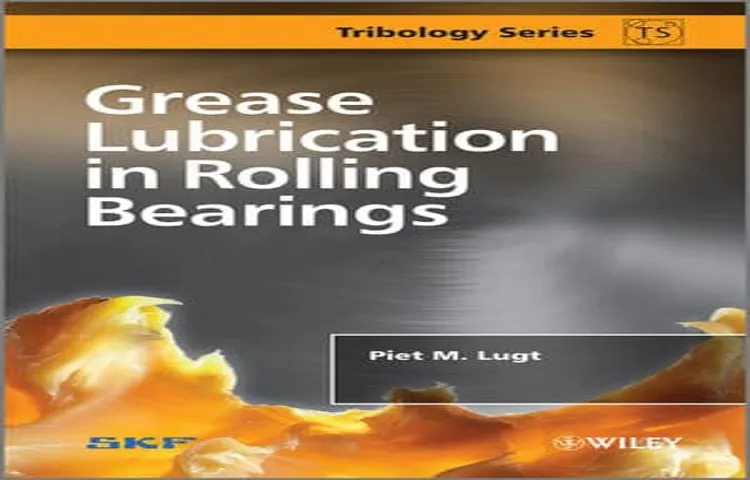
Factors That Affect Grease Quantity
Grease lubrication is a common method for reducing friction and wear in industrial machinery. When using grease as a lubricant, it’s important to ensure that the right amount is applied for maximum effectiveness. There are various factors that can affect the amount of grease required, including the type of equipment, operating conditions, and the amount of wear and tear experienced by the equipment.
For example, high-speed machinery may require a thinner grease, while low-speed machinery may require a thicker grease to ensure adequate coverage. Other factors that can affect grease quantity include temperature, humidity, and the type of bearings or other moving parts being lubricated. To ensure that the right amount of grease is being used, it’s essential to regularly monitor equipment performance and lubrication needs, as well as to consult with experienced lubrication professionals who can provide expert guidance and support.
By taking a proactive approach to grease lubrication, companies can help to ensure optimal performance, reduce downtime and maintenance costs, and extend the lifespan of their equipment.
Calculating Grease Quantity for Bearings
Have you ever wondered how much grease is needed for your bearings to operate at optimal performance? The answer is not as straightforward as you may think. The appropriate amount of grease required for bearings is dependent on various factors, such as the size of the bearing, the application’s operating speed and temperature, and the bearing’s design. Incorrect amounts of grease in the bearing can result in overheating, premature bearing failure, and other negative effects.
As a rule of thumb for general applications, the grease should fill 30-50% of the bearing’s free space, with precision bearings generally requiring lower volumes. This is where knowing the bearing specifications and following the manufacturer’s recommendations come in handy. Proper grease quantity and maintenance ensure the longevity of your bearings, saving you time and money in the long term.
Equation to Determine Grease Quantity
If you are looking to ensure that your bearings operate at optimal levels, calculating the correct grease quantity is essential. There is an equation that can help determine the amount of grease needed in a bearing, which takes into account factors such as the bearing type, size, and speed. By using this equation, you can prevent over-greasing or under-greasing your bearings, both of which can lead to premature failure.
It’s important to note that different types of bearings may require different amounts of grease, so it’s important to consult the manufacturer’s recommendations or seek the advice of a professional. By taking the time to calculate the right grease quantity for your bearings, you can ensure they operate smoothly and efficiently, and extend their lifespan.
Variables and Values in the Equation
Calculating grease quantity for bearings requires understanding the variables and values in the equation. The amount of grease needed depends on factors such as bearing size, operating conditions, and lubrication frequency. It is essential to select the correct grease type and volume to ensure optimum bearing performance.
The process involves determining the bearing’s grease capacity, which is typically specified by the manufacturer, and then applying a suitable lubricant. This can be done manually or using automated lubrication systems, depending on the application’s requirements. Over-greasing or under-greasing can cause bearing failure, leading to costly downtime and repairs.
Therefore, proper grease calculation is critical in maintaining machinery efficiency and productivity. By considering the appropriate variables and values, lubrication professionals can ensure that bearings receive the right amount of grease and enjoy extended service life.
Example Calculation for a Bearing
When it comes to ensuring smooth operation of bearings, one crucial aspect is proper lubrication with the right amount of grease. But how much is the right amount? Let’s say we have a bearing with an inner diameter of 100 mm, an outer diameter of 200 mm, and a width of 30 mm. We can use a formula that takes into account the bearing’s volume and the grease’s density to calculate the necessary grease quantity.
Assuming a grease density of 0.9 g/cm3 and a fill percentage of 30%, we get a grease quantity of 14 cm
However, it’s important to note that this is only a rough estimate, and factors such as operating speed, temperature, and environment must also be taken into consideration to determine the optimal grease amount. By properly calculating and applying grease in bearings, we can prolong their service life and prevent premature failures.
Importance of Proper Grease Quantity
When it comes to properly maintaining bearings, one crucial aspect is knowing just how much grease to use. Too much grease can cause friction and heat build-up, while too little can result in inadequate lubrication and potential damage to the bearing. A good rule of thumb is to fill the bearing cavity to 30-50% capacity with grease.
However, it’s important to note that the optimal amount can vary depending on factors such as bearing size, type of grease, and speed of rotation. In order to ensure that you’re using the correct amount of grease, it’s best to consult the manufacturer’s recommendations or seek guidance from a reputable bearing supplier. By taking the time to properly measure and apply grease, you can maximize the lifespan and performance of your bearings, saving both time and money in the long run.
Effects of Under-Greasing and Over-Greasing
Proper grease quantity is crucial in ensuring smooth and safe equipment operation. Both under-greasing and over-greasing can have detrimental effects on machinery. Under-greasing causes friction, wear, and tear, leading to early wear-out of the components and eventual breakdowns.
On the other hand, over-greasing can cause the grease to escape from the lubrication points, thus resulting in environmental pollution and additional maintenance costs. It can also create a false impression that equipment is adequately lubricated. To ensure the correct amount of grease is used, it is vital to follow the manufacturer’s recommendations and keep a record of previous greasing.
Additionally, incorporating new technologies such as automatic lubrication systems can help to ensure precision in the application of the adequate amount of grease, leading to increased productivity and reduced maintenance costs. In summary, the importance of using the right grease quantity cannot be overstated, and any deviations from the recommended amount can have negative consequences in the long run.
Maximizing Bearing Life with Proper Grease Quantity
Proper grease quantity is vital for maximizing the lifespan of bearings. When too little grease is applied, friction and wear occur, causing damage to the bearings. On the other hand, too much grease can lead to overheating and seal failure.
Therefore, it is crucial to use the correct amount of grease according to the bearing manufacturer’s recommendations. It’s important to remember that not all bearings require the same amount of grease. The size, speed, and load of the bearing, as well as the operating environment, are all critical factors to consider.
By adhering to the proper grease quantity, you can significantly extend your bearings’ life, reduce maintenance costs, and improve overall machine efficiency. Always consult with experts in the industry to identify the right type and amount of grease that can protect your bearings from failure.
Conclusion and Recommendations
In the end, it all boils down to the age-old question of how much grease is enough for a bearing. While some may argue that more is always better, others believe that a well-calculated amount is all it takes to keep those wheels turning smoothly. But one thing is certain: too much grease can lead to overheating and premature failure, while too little can cause excessive wear and tear.
So, it’s all about striking that perfect balance and finding just the right amount of grease for each individual bearing. And like with most things in life, it’s better to err on the side of caution and take things one scoop of grease at a time. After all, a little bit of grease can go a long way in keeping everything running smoothly.
“
FAQs
What is the function of grease in a bearing?
Grease in a bearing serves as a lubricant, helping to reduce friction and wear between the bearing’s moving parts.
How much grease should be used in a bearing?
The amount of grease used in a bearing depends on its size and application. Generally, bearings are filled with 30-50% of their free internal space with grease.
What type of grease is best for a bearing?
The type of grease used in a bearing depends on factors such as temperature, load, and speed. Common types of grease used in bearings include lithium, synthetic, and mineral oil-based greases.
Is over-greasing a bearing harmful?
Yes, over-greasing a bearing can lead to complications such as excessive heat, premature bearing failure, and increased maintenance costs.
How often should grease be applied to a bearing?
The frequency of bearing greasing depends on factors such as the bearing type, application, and operating conditions. Generally, bearings should be re-greased at regular intervals as recommended by the manufacturer.
Can different types of grease be used together in a bearing?
It is not recommended to mix different types of grease in a bearing, as this can lead to inconsistent performance and potentially harm the bearing.
Should bearings be cleaned before greasing?
Yes, it is important to clean bearings before applying grease to help remove any contaminants that could damage the bearing or affect its performance.